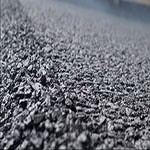
در این پست ابتدا به تعریف آسفالت ماستیک درشت دانه می پردازیم سپس در ادامه به بررسی طرح اختلاط و نحوه اجرای آن می پردازیم.
تعریف آسفالت ماستیک درشت دانه
آسفالت ماستیک درشت دانه، (SMA مخفف Stone Mastic Asphalt) مخلوط آسفالت گرم با دانه بندی گسسته است که از دو بخش سنگدانه ای درشت و ملات پر قیر (مخلوط قیر، فیلر و افزودنی های تثبیت کننده شامل الیاف سلولزی و یا معدنی) تشکیل می شود.
این مخلوط آسفالتی باید ساختار سنگدانه ای درشت با تماس درشت دانه به درشت دانه داشته باشد.
در این آسفالت، درشت دانه ها به مصالح مانده روی الک 4/75 میلیمتر اطلاق می شود، ضمن آنکه از الک 2/36 میلیمتر (شماره 8) نیز می توان برای این منظور استفاده کرد.
دامنه کاربرد آسفالت ماستیک درشت دانه
از آسفالت ماستیک درشت دانه عمدتا به عنوان قشر رویه در مناطق گرمسیر و راه های با آمد و شد زیاد و بار محوری سنگین استفاده می شود.
این آسفالت به دلیل استفاده از مصالح سنگی صد در صد شکسته و مرغوب، مصرف نسبتاً زیاد سنگدانه های بزرگتر از 4/75 میلیمتر در مقایسه با دانه بندی های پیوسته، با ساختار تماس سنگدانه های درشت به یکدیگر که عامل افزایش استحکام و مقاومت آسفالت در مقابل شیار افتادگی و تغییر شکل های دائم می شود و مصرف نسبتاً زیاد قیر، از پایائی و دوام زیادتری نیز برخوردار است.
آسفالت ماستیک درشت دانه، موجب زهکشی آب های سطحی، کاهش پاشش آب ناشی از ایستابی، افزایش ضریب اصطکاک و مقاومت لغزشی رویه راه می شود.
مشخصات مصالح سنگی آسفالت ماستیک درشت دانه
سنگدانه های درشت و ریز مصرفی در آسفالت ماستیک درشت دانه باید سخت، محکم، بادوام، تمیز و مکعبی شکل و صد در صد شکسته باشند.
این مصالح باید با مشخصات جدول های 1 و 2 انطباق داشته باشد.
جدول 1- مشخصات مصالح سنگی درشت دانه
1- استفاده از سنگدانه های با درصد سایش بیشتر در مخلوط های آسفالت ماستیک درشت دانه نتایج رضایت بخش داشته اند.
اما وقتی درصد سایش از 30 تجاوز می کند ، امکان خردشدن سنگدانه ها در مرحله تراکم نمونه آزمایشگاهی و یا تراکم در محل، وجود دارد.
2- آزمایش روی سنگدانه های درشت مانده روی الک 9/5 میلی متر مخلوط مصالح سنگی منطبق با دانه بندی طرح انجام می شود.
جدول 2- مشخصات مصالح سنگی ریزدانه
فیلر معدنی
فیلر معدنی که شامل مصالح رد شده از الک 0/075 میلیمتر است ، از شکستن و آسیاب کردن سنگدانه ها بدست می آید.
از آهک، سیمان و خاکستر بادی نیز می توان به عنوان فیلر فعال در این مخلوط های آسفالتی استفاده نمود .
این مواد در هنگام مصرف بایستی کاملا خشک و بدون ذرات بهم چسبیده باشد.
فیلر بایستی عاری از ناخالصی های آلی و ذرات رس (ریزتر از 0/002 میلی متر) بوده و نشانه خمیری آن از 4 درصد تجاوز نکند.
یادآوری 1- توصیه می شود که از مصرف فیلرهای معدنی با فضای خالی بیشتر از 50 درصد اندازه گیری می شود، در آسفالت ماستیک درشت دانه خودداری شود.
تجربه نشان داده است که این فیلرها موجب افزایش سفتی ملات قیری این آسفالت می شود.
دانه بندی آسفالت ماستیک درشت دانه
دانه بندی این آسفالت باید با یکی از دانه بندی های جدول انطباق داشته باشد.
جدول 3- دانه بندی آسفالت ماستیک درشت دانه
قیر مورد استفاده در آسفالت ماستیک درشت دانه
قیر مورد استفاده در مخلوط های آسفالت ما ستیک باید از نوع قیرهای خالص طبقه بندی شده برحسب درجه نفوذ، و یا عملکردی و یا قیرهای اصلاح شده باشد.
انتخاب قیر مناسب به کیفیت و دانه بندی مصالح سنگی ، شرایط جوی محل پروژه و میزان آمد و شد وسائل نقلیه بستگی دارد.
میزان قیر مصرفی در این مخلوط ها حداقل 6 درصد و معمولا بیشتر از مقدار قیر مخلوط های آسفالتی گرم با دانه بندی پیوسته است.
علت مصرف زیاد قیر در این مخلوط ها، دانه بندی گسسته و مقدار نسبتا زیاد فیلر است.
افزودنی های تثبیت کننده
به منظور جلوگیری از پدیده جدا شدن و یا ریزش قیر آسفالت ماستیک از سنگدانه ها، می توان از تثبیت کننده هایی نظیر الیاف سلولزی و یا معدنی استفاده نمود.
مقدار الیاف سلولزی مصرفی بایستی حداقل 0/3 درصد وزن مخلوط آسفالتی و یا بیشتر باشد.
این الیاف باید با ویژگی های مندرج در جدول 4 مطابقت داشته باشد.
جدول 4- مشخصات الیاف سلولزی
برای الیاف معدنی، میزان مصرف بایستی حداقل 0/4 درصد وزن مخلوط آسفالت باشد تا از پدیده ریزش قیر جلوگیری نماید.
الیاف معدنی باید با مشخصات جدول 5 تطبیق نماید.
جدول 5- مشخصات الیاف معدنی
طرح اختلاط آسفالت ماستیک درشت دانه
طرح اختلاط آسفالت ماستیک با استفاده از دستگاه متراکم کننده چرخشی و مطابق با روش های MP8 و PP41 آشتو، معادل سطح یک روسازی ممتاز انجام می شود و مشخصات فنی آن باید با ویژگی های جدول 6 مطابقت داشته باشد.
جدول 6- مشخصات فنی مخلوط های آسفالت ماستیک درشت دانه با دستگاه متراکم کننده چرخشی روسازی ممتاز
برای راه های با میزان آمد و شد سبک و یا در شرایط آب و هوائی سرد، درصد فضای خالی مخلوط آسفالت متراکم را می توان کمتر از 4 درصد در نظر گرفت، لیکن در هیچ حالتی این میزان نبایستی کمتر از 3 درصد باشد.
1- VCAmix از رابطه زیر محاسبه می شود:
که در آن
Gmb = وزن مخصوص حقیقی نمونه متراکم آزمایشگاهی
GCA = وزن مخصوص حقیقی مصالح درشت دانه
PCA = درصد مصالح درشت دانه در مخلوط
2- VCADRC نیز از رابطه زیر محاسبه می شود:
که در آن:
ɣs = وزن واحد حجم مصالح درشت دانه خشک در آزمایش میله خورده T-19 آشتو برحسب کیلوگرم بر مترمکعب
ɣw = وزن واحد حجم آب ( 998 کیلوگرم بر مترمکعب)
تهیه و اجرای آسفالت ماستیک درشت دانه
تهیه و اجرای آسفالت ماستیک درشت دانه، عمدتاً تفاوت زیادی با اجرای عملیات آسفالت گرم ندارد.
برای انطباق عملکرد این نوع آسفالت با مشخصات مربوطه، رعایت موارد زیر در حین تهیه و اجرا الزامی است:
تولید آسفالت ماستیک درشت دانه
با توجه به درصد نسبتا کم مصالح ریزدانه و درصد زیاد مصالح درشت دانه در این نوع آسفالت در مقایسه با بتن آسفالتی، درجه حرارت مصالح سنگی و در نتیجه مخلوط آسفالتی باید بیشتر از دمای معمولی بتن آسفالتی باشد تا بتواند موجب افزایش کارایی و شکل پذیری آن در مرحله پخش و تراکم شود.
برای این منظور سیستم سوخت واحد گرم کننده مصالح سنگی باید تنظیم و همواره کنترل شود.
قبل از آنکه دمای مصالح سنگی در شروع تولید آسفالت به دمای مناسب برسد، از افزودن قیر به واحد مخلوط کننده خودداری می شود.
برای این منظور ، تسمه نقاله های مصالح و سیستم های متحرک حامل مصالح سنگی از واحد گرمکن کارخانه به واحد مخلوط کن باید پیش گرم شوند.
حداکثر درجه حرارت مخلوط آسفالتی تخلیه شده از واحد مخلوط کن به کامیون، نباید از 175 درجه سانتیگراد تجاوز نماید و حداقل دمای آن هم کمتر از 150 درجه سانتیگراد نباشد.
مصرف افزودنی های تثبیت کننده برای استفاده از قیر نسبتا زیاد، ضمن آنکه افزایش دوام آسفالت ماستیک درشت دانه را تضمین می کند، مانع ریزش قیر از سنگدانه ها و جلوگیری از ایجاد قیر آزاد در مخلوط آسفالت نیز می شود.
در شرایط استفاده از مواد افزودنی تثبیت کننده، این مواد باید در پیمانه های دقیقاً از پیش اندازه گیری شده به واحد مخلوط کن اضافه شود .
تغییر در وزن این مواد موجب تغییر در خواص و کارآئی مخلوط آسفالتی می شود.
در صورتیکه از افزودنی های سلولزی استفاده شود، این مواد نباید قبل از مصرف در معرض رطوبت قرار گیرند.
کاتالوگ و دستورالعمل کارخانه تولید کننده مواد افزودنی تثبیت کننده در ارتباط با دوره زمانی تخلیه مصالح سنگی، فیلر، افزودنی (دوره اختلاط خشک) و نهایتاً مدت زمان اختلاط با قیر (اختلاط تر)، باید دقیقاً رعایت شود.
وقتی دوره اختلاط خشک، شامل افزودن به ترتیب مصالح سنگی، فیلر و مواد افزودنی به واحد مخلوط کن از اندازه لازم (35 تا 40 ثانیه) تجاوز کند، افزودنی ها به شکل پودر سائیده و آمیخته با فیلر در می آید که موجب تغییر کیفیت و کارآئی لازم آسفالت می شود.
تولید مخلوط همگن و یکنواخت تابع مدت زمان اختلاط تر (آغاز زمان افزودن قیر و مدت اختلاط قیر با مصالح، فیلر و افزودنی) است که حدود 10 تا 15 ثانیه می باشد.
مدت زمان اختلاط کامل آسفالت (خشک و تر) قبلاً باید تعیین و در جریان تولید آسفالت مراعات شود.
اولویت اختلاط شامل تخلیه بترتیب مصالح سنگی، فیلر، افزودنیت ثبیت کننده و قیر به واحد مخلوط کن، باید همواره رعایت شود.
در جریان تولید آسفالت ماستیک درشت دانه، از تهیه و تولید نوع دیگری از آسفالت توسط کارخانه آسفالت باید خودداری شود.
حمل آسفالت ماستیک درشت دانه
آسفالت ماستیک درشت دانه، نباید مدت زیادی در سیلوی ذخیره گرم کارخانه نگهداری شود.
کف کامیون های حامل آسفالت باید کاملا تمیز باشد و برای این منظور باید از مواد شوینده مخصوص استفاده کرد.
کلیه کامیون های حامل آسفالت حتی در تابستان و فاصله حمل کوتاه، باید با چادر پوشش شوند.
کامیون های حامل آسفالت که مدت زمان حمل آنها به محل مصرف ، میان مدت و یا دراز مدت باشد، باید به وسایل گرم کننده الکتریکی برای آسفالت مجهز باشند (در موارد مصرف این آسفالت برای تعمیرات، لکه گیری و نگهداری راه و یا در شرایط استفاده از کامیون های مجهز به تسمه نقاله افقی برای پخش و کاربرد آسفالت در موارد خاص).
پخش و کوبیدن آسفالت ماستیک درشت دانه
درجه حرارت آسفالت در موقع تخلیه به فینیشر نباید کمتر از 150 درجه سانتیگراد باشد تا عملیات پخش و کوبیدن آسفالت مطابق مشخصات باشد.
بین مراحل تولید، حمل، پخش و کوبیدن آسفالت باید هماهنگی کامل و برنامه ریزی شده وجود داشته باشد، به نحوی که مجموعه این عملیات بطور مستمر، مداوم و بدون توقف انجام شود.
توقف فینیشر و غلتک ها مجاز نیست، زیرا موجب ایجاد ناهمواری و فرود و فراز سطح آسفالت می شود.
غلتک زنی باید بلافاصله بعد از پخش آسفالت شروع شود و غلتک ها با فینیشر، کمترین فاصله ممکن را داشته باشد.
غلتک های لاستیکی برای کوبیدن آسفالت ماستیک درشت دانه موجب پمپ شدن قیر به سطح نهائی آسفالت و در نتیجه قیرزدگی می شود، لذا استفاده از این غلتکها مجاز نمی باشد.
تجربه استفاده از غلتک سه چرخ فلزی یا دو چرخ ردیف با وزن بیشتر از 9 تن برای کوبیدن آسفالت ماستیک درشت دانه، نتایج رضایت بخشی را نشان می دهد.
کوبیدن زیادتر از اندازه ، موجب قیرزدگی می شود.
حداکثر تعداد عبور غلتک برای تکمیل تراکم، معمولا 6 عبور است که ترجیحاً باید مورد آزمایش قرار گیرد.
برای هر خط فینیشر دو غلتک کفایت می کند.
در صورت استفاده از غلتک های ویبره، عبور اولیه غلتک باید استاتیک، گذرهای بعدی ارتعاشی و گذرهای نهایی استاتیک باشد.
از این غلتک ها در شرایطی که ضخامت آسفالت کم باشد، استفاده نمی شود، زیرا موجب خردشدن سنگدانه های درشت آسفالت می گردد.
توجه : برای آشنایی با انواع غلتک ها در راهسازی اینجا کلیک کنید.
قبل از آنکه دمای آسفالت به 130 درجه سانتیگراد برسد، غلتک زنی باید تکمیل شده و پایان یابد.
حداقل کوبیدگی آسفالت ماستیک درشت دانه مانند آسفالت گرم معمولی ، 97 درصد تراکم نمونه آزمایشگاهی آسفالت است.
برای عبور ترافیک از روی آسفالت ماستیک درشت دانه، حداقل باید 24 ساعت بعد از تکمیل عملیات کوبیدگی، برنامه ریزی شود تا آسفالت، سرد شده و دمای آن کاهش یابد تا موجب حرکت قیر به سطح آسفالت و نهایتاً قیر زدگی نشود.